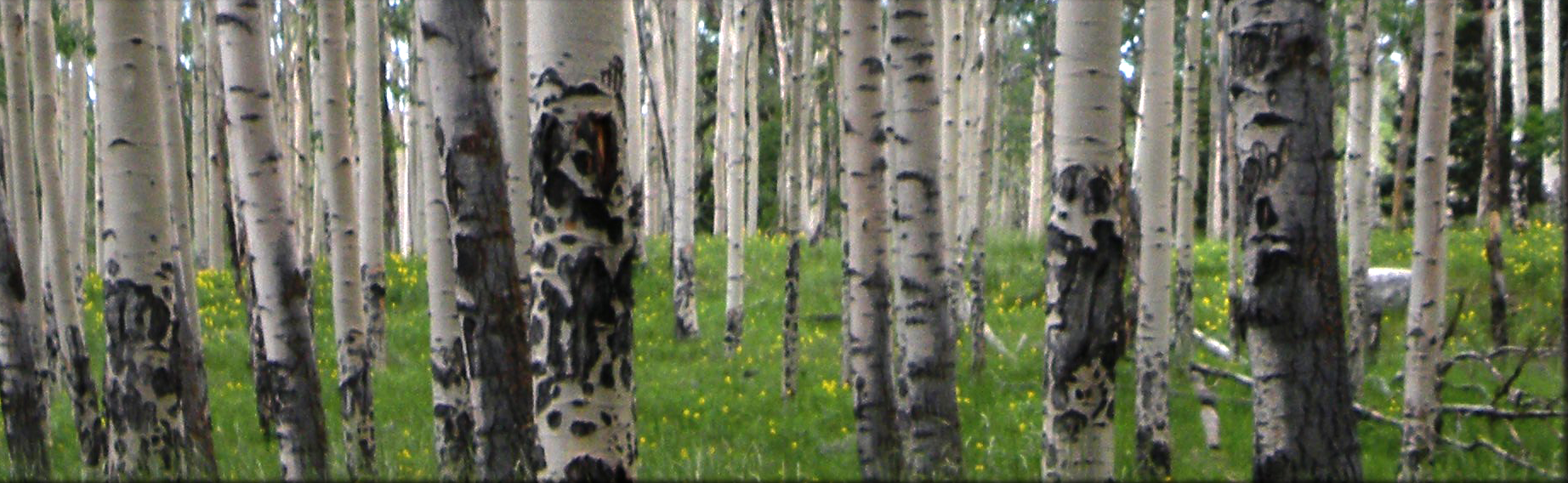
Aspen Bibliography
Low-density boards from wood fiber and plastic resin combinations
Document Type
Article
Journal/Book Title/Conference
Forest Products Journal
Volume
26
Issue
4
First Page
31
Last Page
34
Publication Date
1976
Abstract
Wet-formed boards were made by mixing together methyl-cellulose, saponin, powdered phenolic resin, and wood fiber. Wet mats were dried 24 hours at 60°C and the resin cured at 160°C for 1 hour. The finished boards had densities of 8, 10, and 16 pounds per cubic foot and phenolic resin contents of 20, 30, and 40 percent. Generally, all strength and thermal conductivity properties increased with increasing density. Strength properties changed in proportion to the resin content. Boards made with 30 percent resin content appeared to be a good compromise between strength, thermal conductivity, and amount of resin used. Several fiber furnishes were also investigated for wet-formed boards. The best boards were made with groundwood fiber. Kraft fiber and a blend of groundwood and kraft fibers were less effective. Dry-formed boards were made by spraying pressurized refined aspen fiber with enough liquid phenolic resin to reach a 30 percent concentration. Fibers were air-felted into mats and hot pressed for 20 minutes at 190°C. Dry-formed boards were generally inferior to the wet-formed boards in strength properties, when both had the same resin content and density. They were nearly equivalent in thermal properties. Other techniques for forming low-density boards were investigated. Foaming type phenolic resin, catalyst, blowing agent, and surfactant were mixed with wood fiber. It was nearly impossible to add more than 5 percent fiber to the resin. Foaming action appeared to be inhibited by the fiber. Polystyrene beads were added to wet-formed and dry-formed mats. Distribution of the beads and fibers was very poor. Neither technique yielded any boards that could be evaluated.
Recommended Citation
Myers, G.C., "Low-density boards from wood fiber and plastic resin combinations" (1976). Aspen Bibliography. Paper 4985.
https://digitalcommons.usu.edu/aspen_bib/4985